Conveyorized Gas Ovens BGC 303, BCG 503
Friction Material Manufacturing in the Albany, NY Area
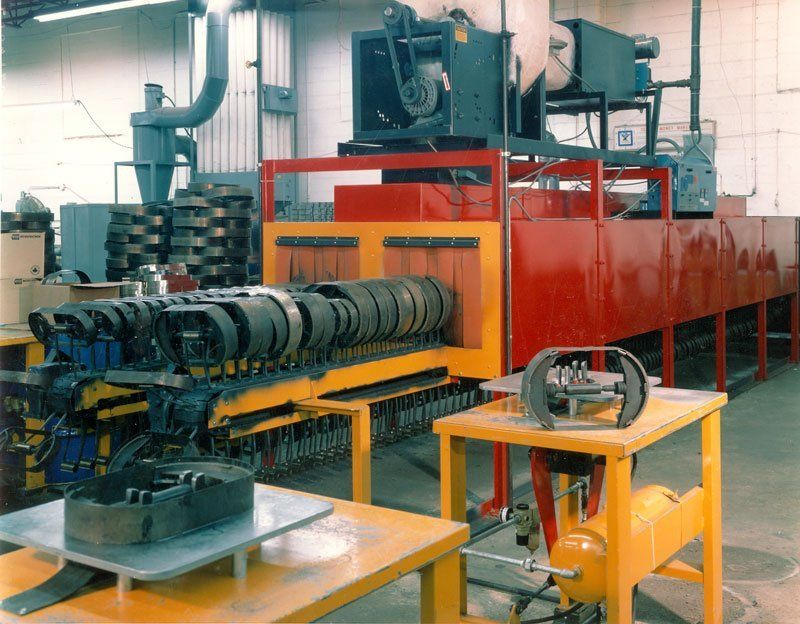
The Raloid Conveyor Ovens are ovens designed specifically for use in the bonding of friction materials. These ovens utilize natural gas, propane, or oil, depending on the model, to fire a positive pressure burner and generate the required heat. Dual fuel models are available. The heat is regulated by a Dual Setpoint Digital Temperature Control. The first setpoint controls the highfire portion of the burner to enable quick initial heating of the oven and of the cold brake shoes as they enter. The second setpoint controls the lowfire portion of the burner, which is cycled as required to maintain the optimum oven temperature. A separate high limit thermostat acts as a safety.
Additionally, a second Digital Temperature Control is used to run the conveyor system. It keeps the conveyor from operating until the correct oven temperature has been reached. If the oven temperature were to later drop, it will stop the conveyor and keep it stopped until the oven has returned to the correct temperature, insuring correct heating of the shoes. Once the oven returns to the correct temperature, the control automatically re-starts the conveyor.
All Raloid Conveyor Ovens have their conveyors individually adjustable to the most efficient speed for the most productive use of manpower. Additionally, the standard conveyor chains automatically return the bonded shoes to the entrance end of the oven, cooling them to a point at which they can be easily handled.
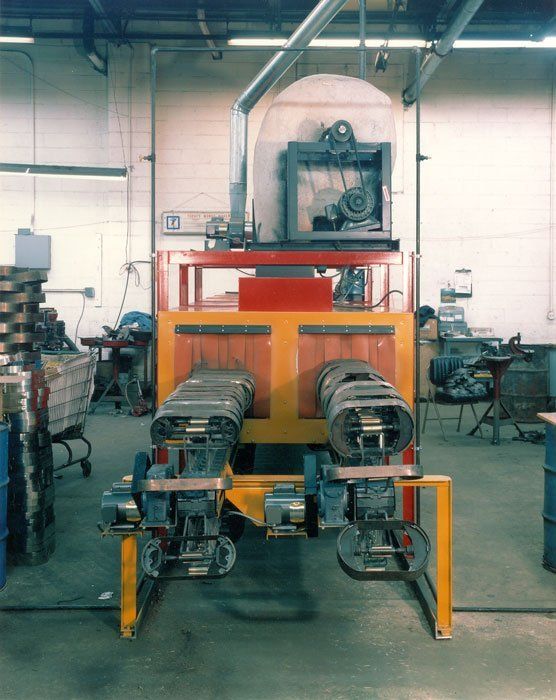
The BCG 303 and BCG 503 CONVEYORIZED GAS OVENS are made in a series of four-foot sections that are connected together and can be easily expanded when increased production is required.
The BCG 303 is a three section conveyorized oven with a capacity of 500 passenger shoes per hour. Two men are used to operate two PT400 Tension Tables that should be placed at the entrance end of the BGC 303 oven where the shoes are automatically returned by the conveyor chains. By using the Raloid Clamping System, each man can clamp and release 250 shoes per hour for a total of 500 shoes per hour, or 4,000 shoes per day.
When increased production is required, two more sections can be added to form the BGC 503 that has a capacity of 1,000 passenger shoes per hour. The two additional sections can be easily installed, but the oven will require some adjustment of the burner for the increased output. With this oven, two men are used at each PT400 Tension Table located at the entrance end of the oven where the shoes are automatically returned by the conveyor chains. Again using the Raloid Clamping System, each man can process 250 shoes per hour, or 1,000 total shoes per hour, or 8,000 shoes per day. This oven can be purchased complete, or it can be made by adding sections to the BGC 303. Both ovens will also bond disc brakes using the DBT88 Disc Pad Adapter for the PT400 Table.
The Conveyorized Gas Ovens are constructed of 20 gauge steel, formed around 1/8” steel sections and mounted on a structural steel frame work. Three inches of fiberglass insulation provides for minimum heat loss and lowest outer surface temperature. The ovens are heated with a pre-mix positive pressure burner, firing into a plenum chamber, and circulated throughout the oven by a three horsepower blower. Maximum efficiency is maintained by positioning the recirculation duct to gain maximum heat transfer. Entrance and exit curtains minimize heat losses.
The two conveyor lines in the BCG 303 and the BGC 503 utilize the normal 3” spacing on the shoe carrier stanchions on each of the lines. Clamping equipment must be provided for these carriers. For extra wide passenger brake shoes, each of the ovens can be fitted with conveyor chains modified to meet your requirements. These modifications would reduce production proportionately. The conveyors provide a specific place for each individual shoe assembly, thus insuring identical exposure to the oven temperature. Clamping fixtures are held to a minimum while insuring the maximum number of shoes per man hour. Also available is a flat wire belt configuration.
The BGC 303 and the BGC 503 are equipped with an automatic ignition system for safety in operation. The main burner gas supply valve will not open until the air flow valves have reached their preset pressure, the oven chamber has been automatically purged, and the pilot has been ignited. If the flame is lost for any reason, this valve instantly and automatically closes. It cannot be reopened until the pilot has been relit.
Specifications:
• BGC 303 – 18’ long, 5’ wide, 9’ high, installed area 90 sq. ft., 500 shoes per hour, 800,000 BTU per hour, 3500 lbs.
• BGC 503 – 26’ long, 5’ high, installed area 130 sq. ft., 1,000 shoes per hour, 800,000 BTU per hour, 4400 lbs.
• Wiring – Main blower is wired 3-phase for your specific voltage- 220/480/575. All control circuits are run on 110 volts.
Options:
• Propane, oil, or dual fuel burners.
• Flatwire belt conveyors.
• Return roller conveyors for flat wire belt system.